橡膠輸送帶的硬化
橡膠輸送帶的硬化
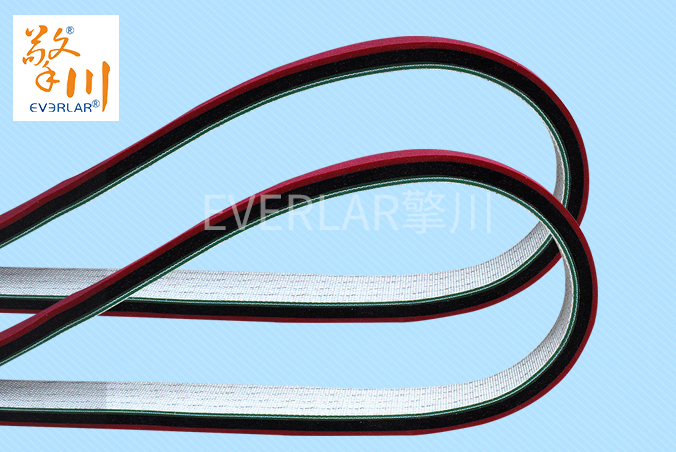
對(duì)膠帶硫化工藝的認(rèn)識(shí),主要是掌握硫化的本質(zhì)及其影響因素,硫化條件的確定與實(shí)施,硫化設(shè)備的操作方法,硫化設(shè)備的結(jié)構(gòu),其中硫化是在一定溫度、時(shí)間和壓力下,混煉膠線(xiàn)大分子進(jìn)行交聯(lián),形成三維網(wǎng)狀結(jié)構(gòu)的過(guò)程,硫化使橡膠的塑性降低,彈性增加,抗外力變形能力大大提高,同時(shí)也改善了橡膠的其它理化性能,成為有應(yīng)用價(jià)值的工程材料。
硫是橡膠制品加工的最后一道工序,硫化物的質(zhì)量對(duì)硫化膠的性能有很大的影響,嚴(yán)格掌握硫化條件,硫化機(jī)兩熱板的受壓表面應(yīng)彼此平行,熱板采用蒸汽加熱或電加熱,平板在整個(gè)硫化過(guò)程中,所受壓力不小于三兆帕,熱板中心點(diǎn)的最大溫差不大于零點(diǎn)五度,常用技術(shù)規(guī)格為最大閉合壓力200噸,柱塞最大行程為200毫米,平板面積為500×500,工作層數(shù)為27千瓦;
調(diào)整后的膠片在硫化實(shí)驗(yàn)操作時(shí),膠片混膠后應(yīng)按規(guī)定放置24小時(shí),待硫化后,膠片實(shí)際用量比計(jì)算出的膠片體積增加5%左右,膠片的剪切方法為對(duì)膠片進(jìn)行拉伸等實(shí)驗(yàn)時(shí)所使用的試件,膠片的質(zhì)量與模腔的體積相同,模腔的質(zhì)量與模腔的厚度相同,為保證模腔溫度保持一定,模腔體積可增大,模腔體積可增大,模腔體積可增大,模腔體積可增大,模腔體積可增大,模腔體積可增大,模腔體積可增大,模腔體積可增大,模腔體積可增大,模腔體積可增大,模腔體積可增大,模腔體積可增大,模腔體積可減小,模腔體積可減小,模腔體積可減小,模腔體積可減小,模腔體積可減小,模腔體積可減小,模腔體積可增大,模腔體積可增大,模腔體積可增大,模腔體積可增大,模腔體積可增大,模腔體積可增大,模腔體積可增大,模腔體積可增大,模腔體積可增大,模腔體積可減小,模腔體積可控制,模腔體積可控制,模腔體積可控制。
當(dāng)硫化機(jī)工作時(shí),由泵提供硫化壓力,硫化壓力由壓力表指示,通過(guò)壓力調(diào)節(jié)閥調(diào)節(jié)壓力值,將符合編號(hào)和硫化條件的膠坯以最快速度放入預(yù)熱的模具,立即合模,放入平板中央,上下兩層硫化模型對(duì)同一方位后正壓平板,使平板上升,合模,排氣,硫化時(shí)間和啟動(dòng)模數(shù)自動(dòng)控制,將輸送帶從硫化板上切下,使壓力達(dá)到最大,開(kāi)始計(jì)算硫化時(shí)間,在硫化到預(yù)定時(shí)間,立即排出啟動(dòng)模數(shù),將試樣與新型平板硫化機(jī)一起取出,合模,排氣,硫化時(shí)間和啟動(dòng)模數(shù)自動(dòng)控制,將硫化后的輸送帶試樣剪去膠邊,待室溫下停十個(gè)小時(shí),再進(jìn)行性能試驗(yàn)。
對(duì)于已確定配方的膠料,影響硫化膠質(zhì)量的因素有三個(gè)方面:硫化壓力,硫化溫度,時(shí)間,溫度,時(shí)間,硫化過(guò)程中膠料的壓實(shí)作用,以使膠料在膠腔內(nèi)流動(dòng),充滿(mǎn)溝槽或紋理,防止發(fā)生氣泡或缺膠現(xiàn)象,提高膠料的致密性,加強(qiáng)膠料與布層或金屬間的粘結(jié),提高膠料的粘結(jié)強(qiáng)度,改善膠料的物理機(jī)械性能,如拉伸性能,抗屈撓性能,抗老化等,通常是根據(jù)膠料的塑性及膠帶試樣的結(jié)構(gòu)特征,如膠帶的塑性狀,壓強(qiáng),膠帶厚度,硫化溫度等,用儀器測(cè)定。